Teamwork at Work: The Journey of LG’s Data-Quickening, Money-Saving Financial Insight Tool
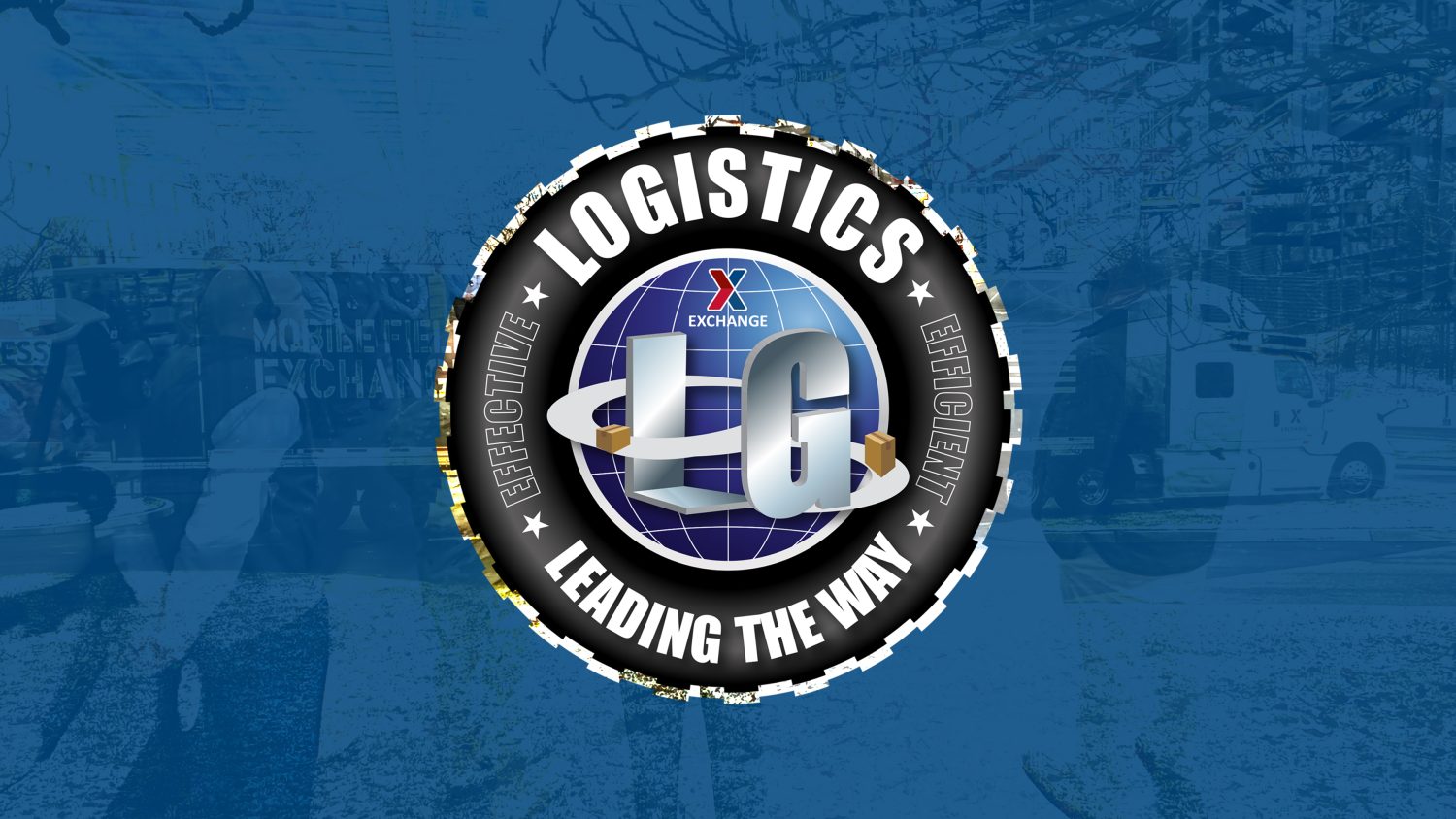
During the peak of the COVID-19 pandemic in 2020, the Exchange was in a cash crunch while still trying to figure out the feasibility of remote work and facing other questions caused by the pandemic.
Karen Stack, Exchange Executive Vice President and Chief Logistics Officer, saw ways that Logistics could reduce expenses. But she needed the directorate’s decision-makers to be able to get information more quickly.
The ultimate solution, a financial insight tool used by distribution-center managers, has saved the Exchange more than $1 million during the past few years.
“We were reviewing operating statements on a monthly cadence,” Stack said. “This timing window needed to be shortened to gain more insight to make course corrections in operations. This tool represents a significant shift in our reporting by giving up-to-date data for distribution center managers and their teams and management to use. The readily accessible up-to-date data in wages, personnel costs, and expenses allows them to make changes as needed or be aware of their current financial status.”
The process used to arrive at the solution was an example of Exchange initiative that can be applied to other directorates’ projects.
Stack assembled a core team that included Exchange Enterprise Project Portfolio Manager Greg Saunders, Senior Logistics Analyst David Saenz, LG Change Manager Maheshi Ruffin, Business Intelligence Chief Mario Garza, BI Systems Architect Brian Simmons, Financial Manager Chuck Martin and Store Ops Analyst James Williamson. Periodically, the team would bring in subject matter experts and core leadership from across the organization to provide valuable input, ensuring a multi-directorate engagement, and effectively utilizing their expertise in a collaborative effort.
“We used a Disciplined Agile approach,” Saunders said. “It’s a project management process that simply states that instead of trying to predefine 100% of your requirements and then try to forecast 12 to 24 months in advance that we’re going to deliver on this date, why not come up with 60% of your requirements, figure out what the market needs a month from now, pick the top two or three things, and deliver them.”
“Then see how the market responds; go back to your requirements list, and you may come back with some new requirements based on feedback from the market,” Saunders continued. “Then pick the next two to five things and deliver them four weeks later. And keep that cycle going.”
On Jan. 29, 2021, the LG Change Management Team released the Financial Insight Tool, which provided the DCMs information in a much more timely manner. Since then, the team has done 17 additional releases, saving the Exchange more than $1 million. The tool provides distribution center managers information as soon as it’s available. Most cycles daily while some cycles weekly or at least midmonth.
“It’s one of those things you look at daily,” said David Hill, Dan Daniel Distribution Center manager. “It provides a great snapshot of how you’re doing and showing trends of where your cost per case is or where your labor hours are, and you can adjust accordingly.”
The tool is a dashboard that shows year-over-year comparisons of labor cost and hours at distribution centers, but also daily labor costs, broken down by types of pay (regular, overtime, holiday, etc.). Numbers can be broken down via individual DCs or totaled together. Beyond the year-over-year comparisons, the tool goes back to 2020 to show how cost trends have changed during the past few years. The tool also breaks down hours by job title.
“Simply put, the tool shows you what levers to pull that will help you,” Hill said. “I can look at labor hours, and if I’ve got some overtime hours that are kind of creeping up, this report will show me whether I need to scale things back based on trends and what we did the previous years. It gives me insight on what to do to keep costs down and productivity high. Prior to this, we could pull the levers but we didn’t always know what effect that was going to have. Now we can see the effects right away.”
David Saenz, the senior logistics analyst who developed the dashboard, said that the biggest challenge was collecting data in a way that could be put on the dashboard. “Making a dashboard itself is fairly simple,” he said. “But getting information from different directorates and getting it to a place where we can put it on the dashboard and display it to the user was more complicated.”
Saunders added that they received some feedback after the first release that helped accelerate adoption by decision-makers in the field. “One of the people on the headquarters team who was looking at this said: ‘I really believe this is an excellent tool; I believe it gives insight that DC managers need and that headquarters needs, but I see an issue here. If I were in the field, as a former DCM, and one of these trends indicated that I had a problem and you reached out to me before I had a chance to fix it, that would create some animosity between us and I wouldn’t want to adopt this tool.’”
The team discussed this feedback, resulting in a policy that unless a trend is out of tolerance, headquarters would not contact a DCM about a trend that is going toward out-of-tolerance until two business days have passed. “Once that policy was made, we had a higher adoption rate,” Saunders said, “because the field knew it has some freedom to act and adjust instead of being immediately contacted to go fix something.”
Saenz added that LG is collaborating with other directorates to continue improving the tool.
“So far, we’ve brought in labor and work hours that we’ve done,” he said. “Now we’re talking in terms of what’s going to happen. What’s the workload going to look like tomorrow or next month? We’re looking at how we can course-correct going into the future.
“That’s in the very beginning stage,” he continued. “It’s something that we’ll discuss as we share this with other directorates. It’s nice to know where you’ve been, but we want to know where we’re going, so that we can better actively manage that aspect of the operation.”
Now THIS is teamwork!